American Plastic Molds are used to produce plastic products. They can be made from many different materials, including low-carbon martensitic aging steel, PMS and corrosion-resistant steel.
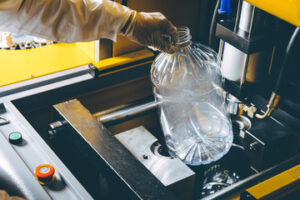
A significant benefit of injection molding is that it reduces production time, because each cycle lasts less than a second. This helps manufacturers to achieve cost savings.
Injection moulding is an excellent method for producing large numbers of dimensionally consistent and uniform plastic parts. It’s especially suitable for producing parts that have a complex design with stringent dimensional tolerances. It also allows for a wide variety of materials to be used, including thermoplastics, thermosets, and elastomers. Despite its many advantages, this manufacturing process is not without flaws. Many of the issues that can arise can be minimized by careful design, but even experienced manufacturers will still occasionally encounter problems.
Some of the more common injection moulding defects are missing sections on the molded part, air pockets in the molten plastic, inconsistent wall thickness, and warping. These issues can be caused by varying temperature, faulty injection speed and pressure, or poor design.
Using a reciprocating screw or plunger, the molten plastic is transferred from the barrel into the mold cavities. The injection pressure is set at about 95% of the total cavity volume. The injection speed is controlled to transfer the molten plastic into the cavities as quickly as possible.
Venting systems allow for the escape of molten plastic during cooling to prevent a vacuum in the mold, and to allow air in during the removal of the molded plastic from the mold. These systems can include parting line vents, groove vents, insert vents, and rod vents.
Another important factor in a successful injection molding process is the clamping pressure, which is the force required to hold the mold halves together. This is generally measured in metric tonnes, and is a combination of the tonnage of the toggle clamping system and a direct lock system (using much larger hydraulic cylinders). Clamping pressure should be optimized to complement the injection pressure and other critical factors such as mold surface area and depth. Failure to do so can result in part defects as well as damage to the equipment itself, such as crushed mold vents, cracked platens, and fracturing of the hydraulic cylinders.
During the injection molding process, the molten plastic is heated by the injection machine to the temperature of its melt point. When the plastic reaches this temperature, it can be injected into the mold cavities using a sprue – a channel connecting the nozzle of the injection machine to the front half of the mold. The sprue contains several runners, which distribute the melted plastic into each cavity. A gate is positioned at the end of each runner, and directs the flow into the individual cavities.
Extrusion Moulding
Plastics are a very common material in a wide range of industrial equipment and daily hardware, and they’re rapidly replacing traditional metal products. A reasonably designed plastic part can often replace multiple metal parts and save cost in terms of labor, transportation, production time and raw materials. In the manufacturing process of these types of products, there are two primary methods of molding that can be used: injection and extrusion.
Injection molding is a very versatile method that combines engineering precision, material science, and design flexibility. However, it requires a high level of craftsmanship and attention to detail during the product design phase to ensure that the final product looks as intended. Injection molds must also be designed with consideration for the coefficient of thermal expansion and contraction of the plastics, which can cause dimensional differences during heating, cooling, forming, and ejection phases. A skilled designer can compensate for these effects by locating any aesthetic detriments in hidden areas of the finished product.
With the extrusion process, hot raw plastic granules are melted into a liquid and forced through a die — much like squeezing Play Doh through a shaped hole. The shape of the die determines the shape of the final product, and this makes it suitable for a variety of shapes including PVC water and sewer pipes, drinking straws, curtain tracks, rods, and fiber optic cables.
This is a very efficient manufacturing process, and it’s ideal when long lengths of identical plastic profiles are needed. In addition, the low tolerance levels of extrusion are a plus when strict mechanical properties are not required.
The disadvantage of this process is that it cannot be as precise as injection molding, especially when it comes to tight diameters. Additionally, the extrusion process can experience significant outlet expansion, which can be challenging to control depending on the type of plastic being produced. However, this can be a benefit for some applications such as thin-walled tubing, where controlled outlet expansion helps maintain a consistent diameter. A skilled extrusion manufacturer can work with designers to optimize the manufacturing process and ensure that the resulting product meets the desired specifications.
Gravity Moulding
Gravity casting is a metal-casting process that relies on the force of gravity to deliver molten metal into a permanent mold. This method can produce parts with complex geometries, thin walls, and fine details, making it ideal for applications where high quality and dimensional accuracy are critical. Gravity casting is also environmentally friendly, as the reusable metal molds eliminate the need for secondary operations and reduce waste.
To begin the process, a pattern is created from wood, plastic, or metal and used to create a mold that accurately reflects the desired final part dimensions. Once the pattern is complete, the two mold halves are securely clamped together and a riser or gating system is installed to control the flow of molten metal into the mold cavity. The gating system must be carefully designed to promote metal flow and ensure that the entire mold cavity is filled. Improper gating systems can cause uneven mold cavity filling, which can result in surface defects and dimensional inaccuracies.
The molten metal is then poured into the mold, using gravity to ensure that it spreads evenly across the entire mold cavity and takes on the precise shape of the cavity. The force of gravity also helps to minimise air pockets and other defects. The molten metal must be poured at the correct temperature to ensure proper solidification and fusion with the sand or other material that comprises the permanent mold.
After the molten metal has completely spread across the mold, it is allowed to cool and solidify until it takes on the form of the final part. Once the cast part has cooled, it is released from the mold and undergoes various post-processing techniques to meet final specifications.
Gravity casting produces parts with high dimensional accuracy, good surface finish, and low porosity. It is also cost-efficient, allowing for large production runs with minimal material waste. As the manufacturing industry continues to evolve, advanced technology such as 3D printing and automation are pushing the boundaries of what is possible with this established process. In addition, advances in mold design and materials are enabling manufacturers to achieve greater levels of precision and consistency.
Rapid Prototyping
An essential part of the product development process, rapid prototyping enables teams to quickly produce high-fidelity prototypes that closely mimic the final product. In addition to reducing the risk of costly production errors and design flaws, it also allows companies to validate their designs with end-user feedback. This helps them focus on the most impactful features, which can reduce product development timelines.
The most common method for rapid prototyping is additive manufacturing (also known as 3D printing). However, other methods like CNC machining can be used to produce prototypes of parts that are too complex for additive fabrication. However, these processes typically require more time and resources to set up and operate than 3D printers.
A plastic mold is a special tool that is used to form molten plastic into the desired shape. The tool is generally made of metal or non-metal, depending on the type of plastic that is being molded. The mold is usually designed using computer-aided design software. The mold design should consider the plastic shrinkage rate, the quality requirements of the molded plastic and the dimensions of the finished product. The design should also take into account the conditions that may affect the performance of the mold, such as rust and corrosion.
The structure of the plastic mold is complex and consists of several parts, such as the punch, head, fine positioning, ejector pin, sleeve and slide device. For example, the sleeve should be designed to allow the molten plastic to be injected into the mold cavity. The sleeve should also be able to hold the injection nozzle and the air runner. The mold should also be able to withstand a high temperature range and have a good corrosion resistance.
Injection molding has many applications in industrial production, including the automotive industry, construction equipment and daily hardware. It is a cost-effective and time-saving method for producing small batches of products with complicated geometries. The proportion of plastic components in such products is increasing, and reasonably designed plastic parts can replace multiple traditional metal ones. However, it is important to choose the correct material for the product’s application. The wrong choice can result in a poor quality plastic product.